Supply Chain Chaos Threatens East Coast After Baltimore Bridge Collapse
Once the port is reopened, trucks will continue to be re-routed around Baltimore, adding time and cost to trips. The aftermath of the collapse of the Francis Scott Key Bridge in Baltimore, Maryland, has raised concerns about disruption to supply chains across the East Coast. The Port of Baltimore remains closed to ships moving in or out until further notice, and officials are facing the task of removing thousands of tons of steel and concrete from the Patapsco River and rerouting ships to other ports across the eastern seaboard. The collapse will lead to short-term congestion and delays at other ports as container ships are diverted and redirected. The White House has pledged to fully reopen the port as soon as possible, and $60 million in emergency funds have been allocated. The impact on supply chains is expected to extend beyond the immediate region, with companies already diverting freight to the West Coast ports and sending freight by rail or truck to East Coast to ensure timely delivery and to mitigate global supply chain risk.
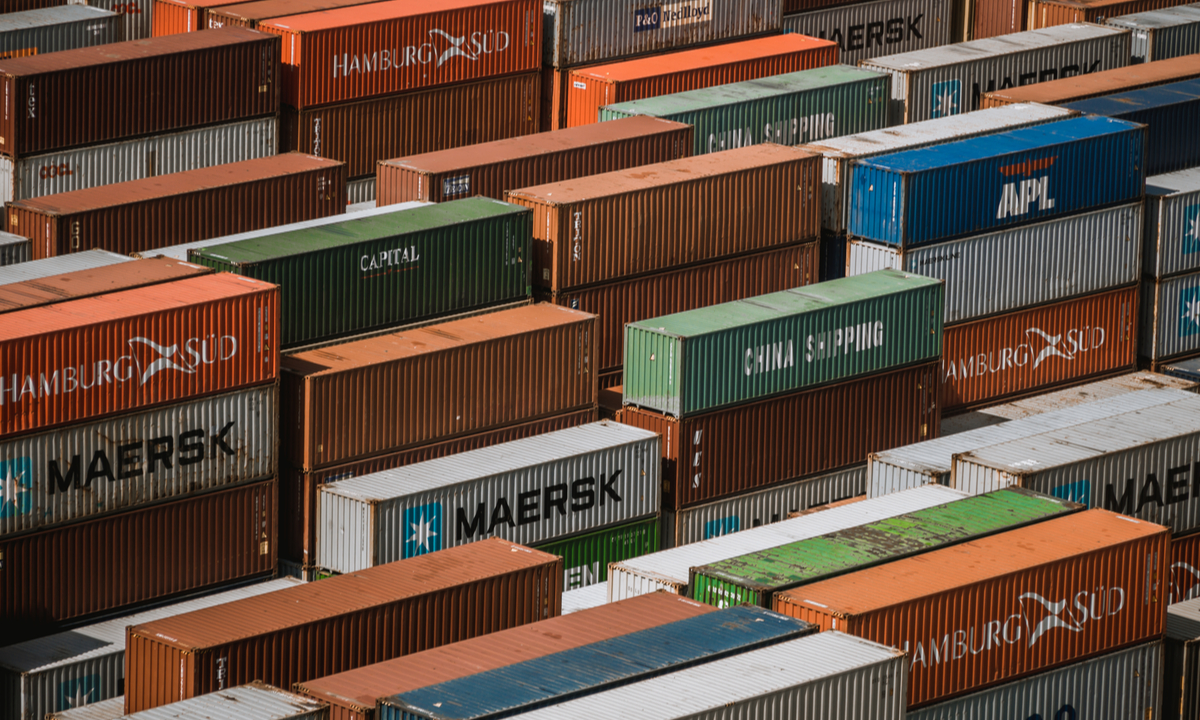
Published : a month ago by PYMNTS in Tech
When supply chains run smoothly, the economies they support do too.
But when even the smallest disruption occurs, supply chains can quickly turn into the equivalent of a daisy chain — where one event sets off a cascading impact down the entire logistics value chain.
Experts fear that this is what could happen up and down the East Coast as businesses and shippers try to manage the fallout from the March 26 collapse of Baltimore’s Francis Scott Key Bridge as a result of a cargo ship collision.
“The impacts to the local region will be significant for several months or years until the bridge is rebuilt,” Lisa Anderson, founder and president of LMA Consulting Group, told PYMNTS in an interview. “Even once the port is reopened, trucks will continue to be re-routed around Baltimore, adding time and cost to trips from the port and through the Baltimore area.”
The Port of Baltimore itself remains closed to ships moving in or out until further notice, and officials are now faced with the task of removing the thousands of tons of steel and concrete clogging Maryland’s Patapsco River, while at the same time navigating the logistics of rerouting Baltimore-bound ships to other ports up and down the eastern seaboard.
The White House has said in a statement that it will “move heaven and earth” to fully reopen the port as soon as possible, and $60 million in “quick release” Emergency Relief funds for the Maryland Department of Transportation have already been made available.
The U.S. Coast Guard opened a temporary alternate channel Monday (April 1) for vessels that are helping with the cleanup effort.
“The most critical timeframe is clearing the bay to reopen the port, which could take weeks,” Anderson said. “This will impact the ninth biggest port in the U.S. and 3,200 sites involved in logistics, distribution and warehousing nearby the port and bridge as well as local businesses.”
See also: Disruptions Happen: Baltimore Bridge Collapse Underscores Need for Operational Agility
Fallout Will Extend Beyond the Port’s Immediate Vicinity
While supply chains have evolved to become more resilient in the face of disruptions, the magnitude of this event will test their capabilities. Although adjustments and adaptations may mitigate some of the immediate challenges, the effects are expected to linger for months or even years until the bridge is rebuilt and normalcy restored.
While the Port of Baltimore remains impassable to ships and maritime traffic, it is open to ground vehicles and trucks. The Maryland Transportation Authority has the most up-to-date traffic alerts and information regarding transportation routes and detours in and around Baltimore for commercial ground transport.
From an East Coast supply chain perspective, the collapse of the bridge will lead to short-term congestion and delays at other ports as container ships are diverted and rerouted. Baltimore’s status as a hub for handling automobiles and trucks further exacerbates the situation, amplifying the impact on those industries.
“Companies are starting to divert at least a portion of their freight to the West Coast ports and are sending freight by rail or truck to the East Coast to ensure timely delivery and to mitigate global supply chain risk,” Anderson said. “Once they transition routes, they might decide to stick with the new routes.”
But the fallout could stretch beyond the immediate region.
“From a global supply chain perspective, the bridge collapse has the potential to divert container ships from Northeast Asia to the West Coast ports (instead of to the East Coast ports) as shipping companies are already experiencing capacity issues in the Panama Canal due to drought issues and safety issues in the Suez Canal due to the Iran-backed Houthi rebels attacking ships,” she added.
Supply Chain Resiliency Is Being Put to the Test
Although disastrous events can trigger repercussions around the globe, they have also forced companies to invest in upgrades that have resulted in smoother procurement and supply chain efficiencies, rather than relying solely upon “just in time” delivery workflows.
PYMNTS Intelligence data in the report “Digital Payments: Modernizing Procurement Processes” revealed that corporations learned lessons from the supply chain disruptions triggered by the global COVID-19 pandemic. As a result, many of those companies took steps to improve their supply chain procedures.
“Overall, [the collapse] will add time and cost to the supply chain with the diversions, re-routing, extra transportation costs and fuel charges,” Anderson said. “Whether these effects will be felt depends on your position in the supply chain and the proactive strategies taken to mitigate risk and manage cost.”
For all PYMNTS B2B coverage, subscribe to the daily B2B Newsletter.
Topics: Traffic